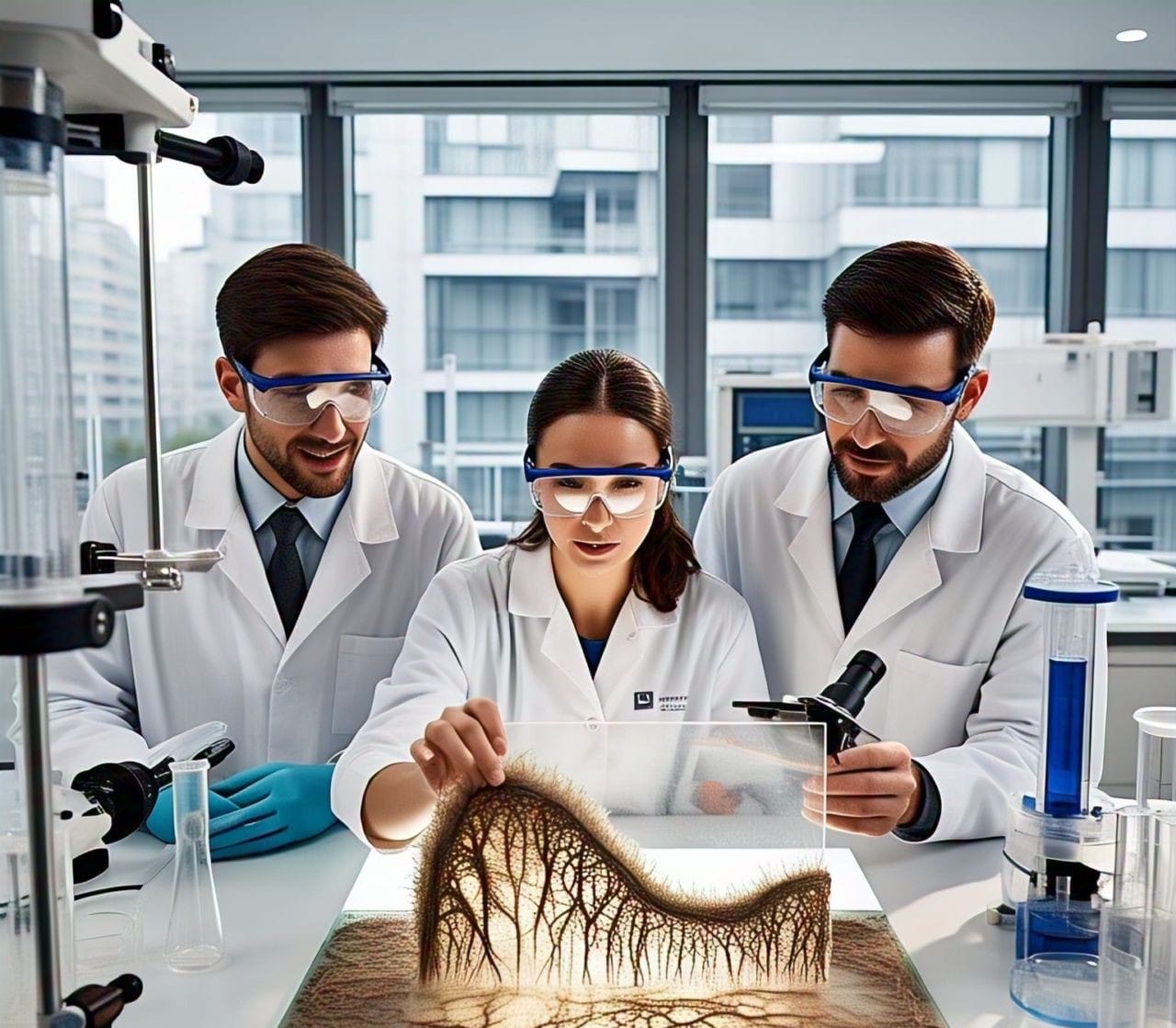
A Living Revolution in Building Materials
Imagine a world where buildings can heal their own cracks, much like human skin. This groundbreaking concept is now a reality, thanks to engineers who’ve developed a living building material using fungal mycelium and bacteria. Published in Cell Reports Physical Science, this innovation from Montana State University offers a sustainable alternative to carbon-heavy concrete—a material responsible for 8% of global CO₂ emissions. Let’s explore how this self-repairing biomaterial could reshape construction.
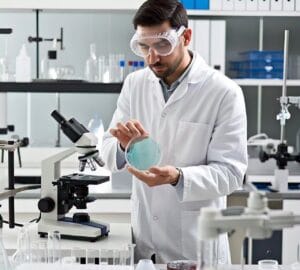
What Is This Living Material Made Of?
At the heart of this innovation are two biological components: fungal mycelium and bacteria.
- Fungal Mycelium: Acting as a scaffold, mycelium—the root-like network of fungi—provides structural integrity. Researchers used Neurospora crassa, a fast-growing fungus, to create complex internal architectures, even mimicking structures like cortical bone.
- Bacteria: Embedded within the mycelium, bacteria drive biomineralization, a process where living organisms produce minerals. This synergy creates a material that’s both robust and adaptable.
Unlike traditional concrete, which requires energy-intensive production (e.g., heating limestone to 1,450°C), this biomaterial is manufactured at low temperatures, drastically reducing its carbon footprint.
Self-Healing Capabilities: A Month-Long Lifespan
Previous biomaterials struggled with short viability periods—often just days or weeks. However, this fungal-bacterial hybrid remains active for over a month, a significant leap forward.
While self-repair and environmental remediation (e.g., cleaning contaminants) weren’t directly tested, the extended lifespan of the bacteria opens the door to these functionalities. As lead researcher Chelsea Heveran explains, “The longer cells live, the more time they have to perform useful functions.” This durability positions the material for real-world applications, where sustained activity is critical.
Why This Matters: Environmental and Practical Benefits
1. Reducing Carbon Emissions
Concrete’s environmental toll is staggering. By replacing it in non-load-bearing applications (e.g., insulation, façades), this biomaterial could curb emissions while maintaining structural needs.
2. Versatile Applications
The mycelium scaffold allows engineers to design intricate geometries, enabling customization for specific uses. Potential applications include:
- Self-Repairing Structures: Automatically sealing cracks to prevent water damage.
- Pollution Remediation: Bacteria could break down toxins in contaminated sites.
- Temporary Construction: Biodegradable materials for events or disaster relief.
3. Energy-Efficient Production
Low-temperature manufacturing aligns with global sustainability goals, offering a blueprint for eco-friendly material science.
Challenges and the Road Ahead
While promising, the material isn’t yet ready to replace concrete entirely. Current limitations include:
- Strength: Biomineralized materials lack the compressive strength of concrete for heavy-duty use.
- Scalability: Mass production methods need refinement to compete with established industries.
The team’s next steps focus on enhancing cell longevity and optimizing manufacturing processes. As Heveran notes, “We’re working to improve properties for greater usage.” Collaborations with industries could accelerate adoption, particularly in sectors prioritizing sustainability.
Conclusion: Building a Greener Future
This living material represents a paradigm shift in construction. By harnessing biology, engineers are paving the way for structures that heal, adapt, and minimize environmental harm. While challenges remain, the potential to reduce CO₂ emissions and redefine architectural design is immense.
As research progresses, we may soon see cities where buildings aren’t just static structures—they’re living ecosystems. The fusion of mycelium and bacteria is more than a scientific breakthrough; it’s a step toward harmonizing human innovation with nature’s wisdom.
1. The Science of Biomineralization: How Bacteria “Grow” the Material
The bacteria embedded in the fungal scaffold perform biomineralization, a process where microbes secrete enzymes that trigger chemical reactions, depositing minerals like calcium carbonate into the material. This mimics how seashells or coral reefs form in nature. Over time, these minerals reinforce the mycelium structure, enhancing its durability. Researchers are exploring tweaking bacterial strains to produce stronger or faster-forming minerals, which could improve the material’s load-bearing potential.
2. Why Neurospora Crassa? The Fungus Behind the Innovation
The choice of Neurospora crassa isn’t random. This fungus:
- Grows rapidly, colonizing substrates in days.
- Self-heals its own mycelial networks when damaged.
- Thrives in diverse environments, from tropical climates to lab settings.
Its resilience and adaptability make it ideal for scalable production. Future strains could be genetically modified to optimize growth speed or mineral affinity.
3. Bio-Inspired Design: Learning from Nature’s Blueprints
The material’s bone-like structure isn’t just a coincidence. By mimicking cortical bone (the dense outer layer of human bones), engineers leverage nature’s genius for balancing strength and weight. Similar bio-inspired approaches could lead to:
- Honeycomb geometries for lightweight insulation.
- Branching networks for efficient load distribution in walls.
4. Beyond Buildings: Unconventional Applications
While construction is the primary focus, this material’s versatility opens doors to niche uses:
- Space habitats: NASA explores mycelium for growing structures on Mars.
- Wearable tech: Flexible, self-repairing sensors or biodegradable electronics.
- Art installations: Living sculptures that evolve over time.
5. Competing with Hempcrete and Bamboo
Compared to other sustainable materials:
Material | Pros | Cons |
---|---|---|
Fungal-bacterial | Self-healing, low-energy production | Lower strength (for now) |
Hempcrete | Good insulation, carbon-negative | Requires binders (e.g., lime) |
Bamboo | High tensile strength, rapid regrowth | Limited to specific climates |
This material’s unique edge is its autonomous repair capability, reducing long-term maintenance costs.
6. The Role of Circular Economy and End-of-Life
Unlike concrete, which generates rubble, this biomaterial is fully biodegradable. At the end of its lifespan, it can:
- Decompose naturally, enriching soil.
- Be composted into fertilizer.
- Serve as feedstock for new material batches, closing the loop.
7. Industry Momentum: Who’s Already Using Mycelium?
Startups like Ecovative Design and MycoWorks commercialize mycelium for packaging, leather, and insulation. While their products aren’t “alive,” this research bridges the gap by integrating living cells for dynamic functionality. Partnerships with such companies could fast-track real-world adoption.
8. Regulatory Hurdles and Safety
Before hitting the market, the material must meet building codes. Key questions include:
- Fire resistance: Can biominerals improve flame retardancy?
- Moisture tolerance: How does prolonged humidity affect fungal activity?
- Pathogen risks: Ensuring bacteria/fungi strains are non-toxic and non-invasive.
Early trials in controlled environments (e.g., green roofs) could build regulatory confidence.
9. The Role of AI and 3D Printing
Future iterations might combine this material with:
- 3D printing: Layer-by-layer fabrication of complex, custom shapes.
- AI-driven design: Algorithms optimizing mycelium growth patterns for strength.
- Smart sensors: Embedding bacteria to detect and repair micro-cracks autonomously.
10. Call to Action: How Readers Can Support the Shift
- Advocate: Urge local governments to incentivize green materials.
- Experiment: DIY enthusiasts can explore mycelium kits for small projects.
- Invest: Follow startups in biofabrication for crowdfunding opportunities.
Final Thoughts: A Living Legacy
This fungal-bacterial material isn’t just a tool—it’s a testament to humanity’s ability to collaborate with nature. As research accelerates, we inch closer to cities where buildings breathe, heal, and return to the earth without a trace. The future of construction isn’t just sustainable; it’s alive.